
Smart solutions for a sustainable future
Ultimate UD-tape for high performance products
UD-automated is the expert when it comes to high performance thermoplastic UD-tape. Do you need the best value for money? UD-automated has the solution for you!
With our proprietary technology, UD-automated is able to provide thin, high tensile strength UD-tape or products tailored to your specific specifications. Our brand UD-A TAPE™ stands for ultimate value in your production process.
Why UD-Automated?
UD-Automated is highly equipped to meet or even exceed your specifications. UD-automated has the flexibility to process many different fiber and matrix types. Please inquire about possibilities for your tailor made product.
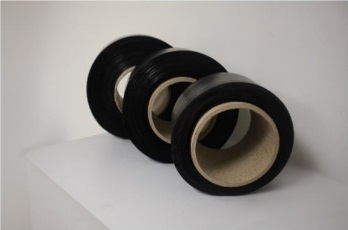